Product Costing is the process of determining the total cost to produce a product. This includes all expenses related to materials, labor, and overhead. In a manufacturing context, it helps businesses understand how much it costs to make each item, which is crucial for pricing, budgeting, and financial analysis. In SAP, product costing integrates with various modules to provide a detailed and accurate cost structure for each product produced.
Product Costing is part of the Controlling (CO) module in SAP, not the Financial Accounting (FI) module. While it involves financial data, it primarily focuses on internal management reporting, cost control, and decision-making processes within the organization, which are key functions of the Controlling module
The best way to calculate product costs is by considering:
- Direct Costs: Costs directly tied to production, such as raw materials and labor.
- Indirect Costs (Overheads): Costs that support production but aren’t directly tied to it, like utilities and depreciation.
- Fixed Costs: Costs that remain constant regardless of production volume, such as rent or salaries.
- Variable Costs: Costs that fluctuate with production levels, like materials and labor.
Costs in a manufacturing company:
Personnel Costs:
- Direct Labor: Wages of blue-collar workers directly involved in the production process.
- Indirect Labor: Salaries of support staff such as quality control, maintenance, production team managers (white-collar), and supervisors.
Non-Personnel Costs:
- Non-BOM Material Consumption: Costs for consumables that aren’t part of the Bill of Materials, like lubricants, cleaning supplies, and minor tools.
- Shop Floor Expenses: Costs related to the day-to-day running of the production floor, including safety gear, small equipment, and waste disposal.
Fixed Expenses:
- Departmental Overheads:
- Purchasing: Manages the procurement of raw materials and components, with overheads covering salaries, office expenses, and procurement systems.
- Warehouse and Inbound Logistics: Handles storage and internal movement of materials, with costs related to facility maintenance, handling equipment, and staff wages.
- Design and Engineering (excluding R&D): Focuses on product design and engineering, contributing to overhead through salaries, design software, and prototyping expenses.
- Quality Control (QC) and Testing: Ensures products meet quality standards, with overhead costs including staff salaries, testing equipment, and materials.
- Production Planning and Management: Manages production schedules and operations, with overheads covering management salaries, planning tools, and administrative support.
- Human Resources (HR): Manages recruitment, training, and employee benefits, contributing to overhead through HR staff salaries and training programs.
- Information Technology (IT): Supports all IT infrastructure, with costs including salaries, software licensing, and IT maintenance.
- Administrative and General Management: Oversees general administration, with overheads including executive salaries, office supplies, and maintenance.
- Maintenance: Ensures machinery and equipment are operational, with costs for maintenance staff, spare parts, and tools.
- Sales and Marketing: Responsible for promoting and selling products, with overheads including salaries, advertising costs, and customer outreach expenses.
- Finance: Manages the company’s financial activities, contributing to overhead through salaries, financial software, auditing fees, and financial management expenses.
- The Research and Development (R&D) department plays a pivotal role in a manufacturing company by driving innovation and improving products and processes, contributing to departmental overheads through costs such as salaries of engineers and scientists, research materials, lab equipment, software, and expenses related to testing, trials, and regulatory compliance
Depreciation (Indirect):
- Indirect Equipment Depreciation: Depreciation of machinery, tools, and equipment used in support departments like maintenance, quality control, and warehouse operations.
- Office Equipment Depreciation: Depreciation on computers, furniture, and other office equipment in departments that support production indirectly, such as purchasing and production management.
Method of Product costing
To calculate the labor rate, we’ll consider the following steps:
- Total Working Days: Calculate the total working days in a year.
- Available Working Days: Deduct weekends, official holidays, training, and meeting days.
- Effective Working Days: Adjust for efficiency.
- Total Working Hours: Convert effective working days into hours.
- Labor Rate: Calculate the rate per hour based on the salary and total effective working hours.
Step 1: Total Working Days in a Year
- There are 365 days in a year.
- Assume a 5-day work week, so there are 104 weekend days in a year.
Working Days = 365 – 104 = 261 days
Step 2: Available Working Days
- Official holidays: 20 days
- Assume internal training and meeting days to be 10 days.
Available Working Days = 261 – 20 – 10 = 231 days
Step 3: Effective Working Days (Adjusted for Efficiency)
- Efficiency: 80%
Effective Working Days = 231 * 0.8 = 184.8 days
Step 4: Total Working Hours
- Assuming an 8-hour workday:
Total Working Hours = 184.8 * 8 = 1478.4 hours
Step 5: Labor Rate
- Total salary: 12 lacs for two laborers
Labor Rate per Hour = 12,00,000/1478.4 = INR 811.63 per hour
So, the minimum labor rate would be approximately INR 811.63 per hour.
To convert the labor rate from per hour to per minute:
There are 60 minutes in an hour.
Labor Rate per Minute = 811.63 / 60 = INR 13.53
So, the minimum labor rate would be approximately INR 13.53 per minute.
Non Personnel costs
1. Machine Maintenance
- Description: Costs for the upkeep and repairs of machinery used on the shop floor.
- Example: Regular servicing, parts replacement, lubrication, etc.
- Annual Cost: INR 1,00,000
2. Consumables
- Description: Materials used during production that are not part of the final product but are essential for the manufacturing process.
- Example: Cutting tools, lubricants, welding rods, coolants.
- Annual Cost: INR 1,20,000
3. Utilities (Specific to Production)
- Description: Electricity, water, and other utilities used by machines and equipment on the shop floor.
- Example: Power consumption by CNC machines, air compressors, lighting specific to production areas.
- Annual Cost: INR 1,50,000
4. Tooling Costs
- Description: Costs for tools and equipment required for specific tasks in the production process.
- Example: New tools, jigs, and fixtures.
- Annual Cost: INR 75,000
5. Safety and Compliance
- Description: Costs for ensuring that the shop floor meets safety regulations, including safety gear for workers, compliance with environmental standards, etc.
- Example: Safety equipment, fire extinguishers, ventilation systems.
- Annual Cost: INR 50,000
6. Subcontracting Costs (Related to Shop Floor)
- Description: Costs incurred when specific shop floor tasks are outsourced to external contractors.
- Example: Outsourced machining or painting processes.
- Annual Cost: INR 1,00,000
Example Calculation for Total Shop Floor Non-Personnel Costs.
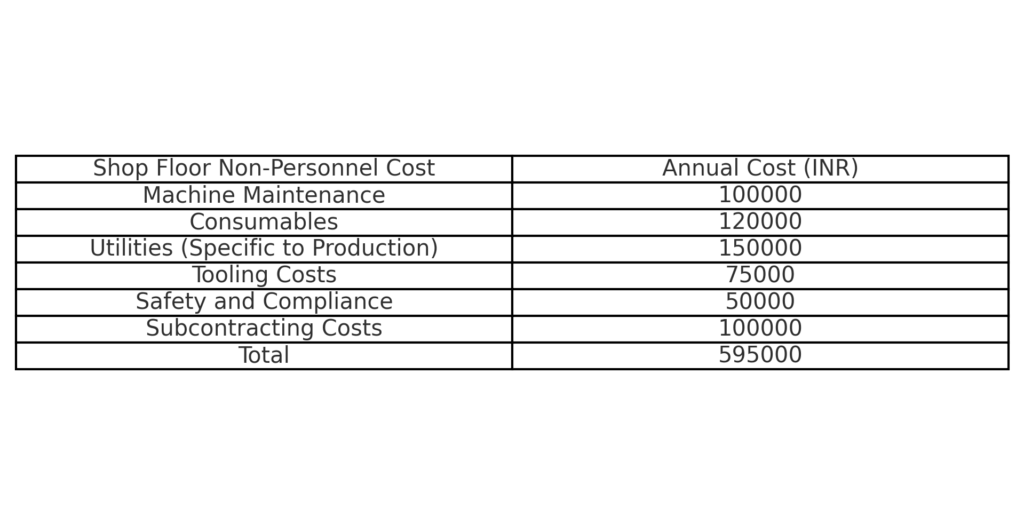